Barilla-Transporeon: Partnership for Global Food Logistics
A platform is born to integrate existing systems, with the aim of bringing Made in Italy to 100 countries
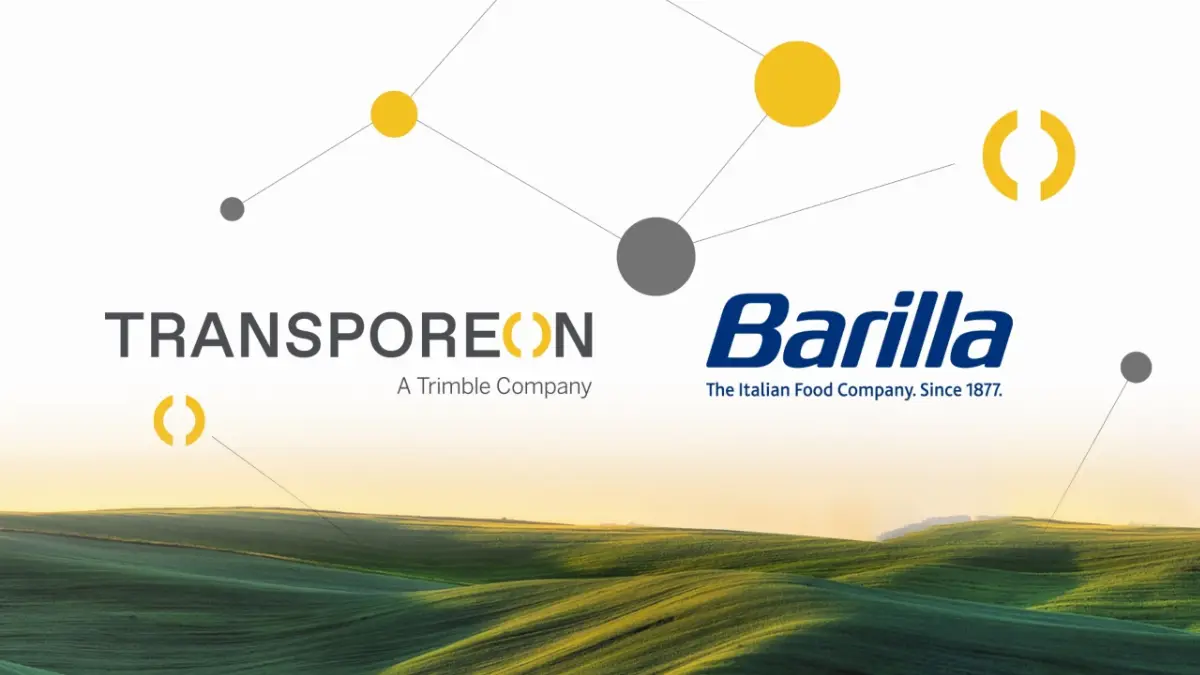
Barilla: a Made in Italy company with an international reach, opens the doors of its “City of Pasta” in Pedrignano (PR), to host a live visit in collaboration with its partner Transporeon - a Trimble company.
Welcoming guests in the “Ringo” conference room was Roberto Magnani , Vice President Logistics of Barilla Group, who also introduced the speeches of Gianluigi Mason – Logistics Italy Director Barilla Group - and Davide Busato – Logistics Systems and Processes Ass. Manager. The morning then continued with a visit to the Pedrignano site, the largest automated warehouse in the world in the food sector, with a total surface area of 60,000 m².
The partnership between the food giant and the transport management platform began in 2014 - more than 10 years ago - when Barilla reorganized its logistics assets and consequently transformed the entire management of operations. “65% of the logistics budget is dedicated to transport and specifically 50% of our loads travel by road, which is why it is essential to support our national - and international - network by choosing innovative solutions such as those proposed by Transporeon to best manage our volumes that reach 600 thousand tons per year”, says Gianluigi Mason .
Following a reorganization of its logistics configuration, linked to the expansion of the multinational - which currently has about 110,000 Full Truck Load shipments per year in 100 countries - Transporeon entered the scene, which had the burden of finding solutions capable of streamlining the process of assigning loads to carriers. Transporeon has been able to carefully follow the growth phases of Barilla in these 11 years, simplifying and speeding up the procedures related to the management of transport and warehouses. For example, thanks to the Time Slot Management solution, Transporeon has facilitated the optimization of internal processes by harmonizing the flow between the warehouse and loading bays and reducing waiting times by 20%, so much so that the platform's solutions are now used in all the Italian plants and a good part of the European ones of the group.
The Transport Assignment feature, on the other hand, allows you to avoid the manual management of assigning transports to carriers, which is extremely time-consuming and inefficient in terms of operational efficiency. In fact, processes such as assigning the carrier to the most appropriate route, analyzing geographic coverage and the best routes, evaluating the suitability of carriers and verifying guaranteed delivery times are just some of the parameters to be checked to evaluate carriers; evaluations now provided by the platform.
“Over the years we have implemented several Transporeon solutions, so much so that today we rely on the modularity of this platform to assign trips to each carrier, from Italy to the rest of the world. Since 2022 we have also been using “Rate Management” which allows us to optimize the route assignment process. In the event of unavailability of the chosen carrier, the platform automatically finds a backup solution, giving us the ability to manage any critical issues in real time: all Barilla transports follow this allocation principle, with an accuracy rate that exceeds 95%”, says Busato . “Rate Management is particularly useful when there is a large diversification of carriers and routes, as in our case. This tool allows us to be open to all the possibilities that the market offers and makes the work of planners simpler and more efficient”.
The information comes from the Transporeon platform directly to Barilla's Logistic Control Tower, to then be consolidated; at this point the routes will be assigned according to the No Touch Order method for those already contracted, or Best Carrier for spot trips. "Transporeon is not a software but a platform capable of integrating perfectly with systems already in use and collaborating with them, acting as a communication bridge between industry, carriers and retailers. An important added value is undoubtedly the possibility of customizing each assignment parameter: our team has worked and is working closely with Barilla to create an ad hoc solution, designed to guarantee the right transport capacity every day following precise route-carrier matching logics", says Andrea Chiaravalli , Account Manager of Transporeon.
The success of this partnership highlights the importance of digital transformation in the logistics sector, not only to optimize costs and operational efficiency, but also to ensure the continuity and reliability of distribution on a global scale. In an increasingly interconnected world, Barilla's innovative approach to supply chain management is crucial to maintaining its leading position in the international food market, bringing Italian tradition to the tables of millions of families around the world.
EFA News - European Food Agency